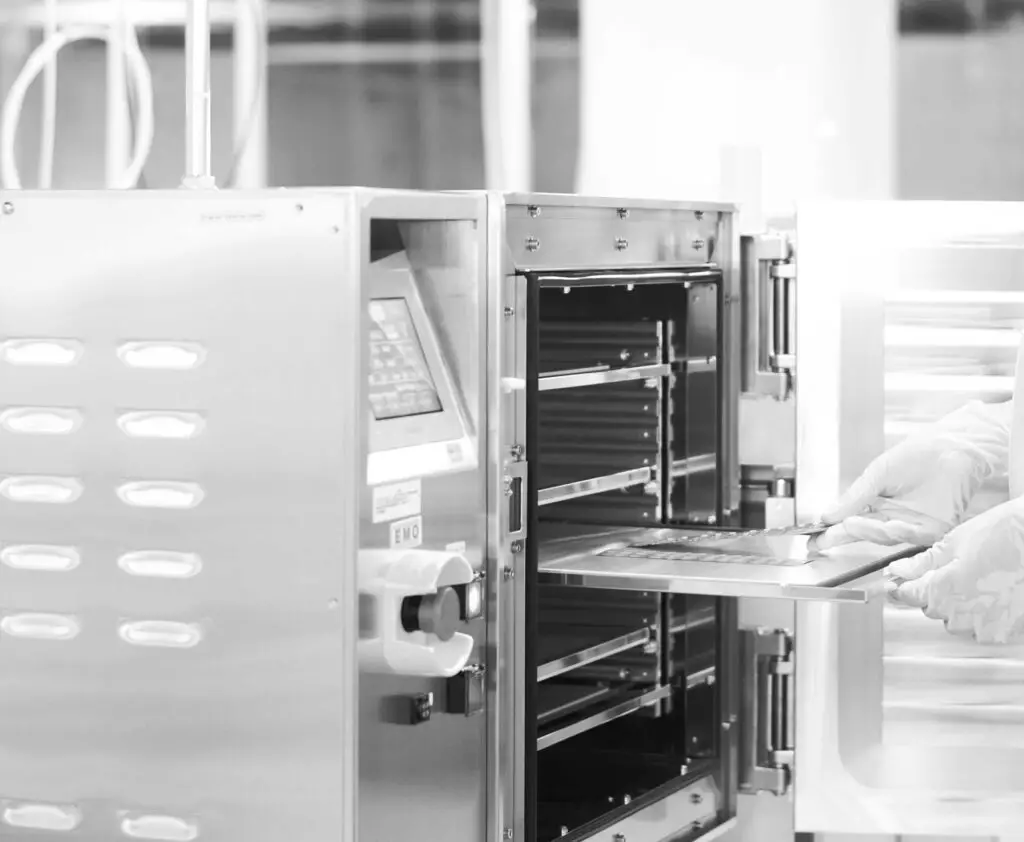
Samco Plasma Cleaning technology offers versatile surface treatment solutions using a range of plasma processes, including PE (Plasma Etching), RIE (Reactive Ion Etching), and DS (Downstream). These processes are suitable for cleaning and modifying the surface properties of various materials, such as plastics, metals, and microelectronics, by improving wettability, removing contaminants, and enhancing adhesion. With options for multi-shelf processing and adjustable electrode spacing, the systems accommodate both R&D and production needs. The intuitive user interface and customizable plasma modes ensure optimal results for a wide range of applications, from semiconductor packaging to medical devices and microfluidics fabrication.
Plasma treatment
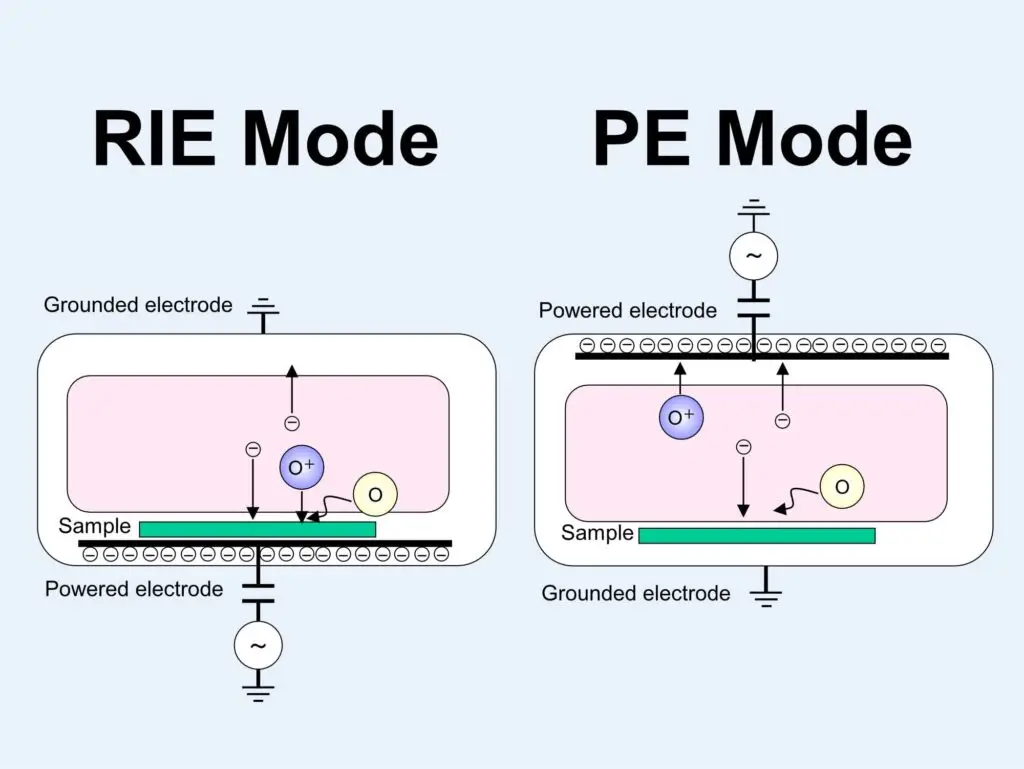
Samco’s plasma cleaning systems provide highly effective solutions for a variety of surface treatments, including cleaning, activation, modification, and photoresist removal. Our systems offer versatile process options using O₂ and argon plasmas, with modes such as Plasma Etching (PE) and Reactive Ion Etching (RIE) to cater to different substrate requirements.
PE mode utilizes oxygen radicals to remove organic contaminants, ensuring damage-free processing ideal for delicate substrates. RIE mode combines ion bombardment and radical effects for faster, more aggressive cleaning, making it suitable for metal surfaces and high-precision applications. These dual mechanisms—physical sputtering by ion bombardment and chemical reactions breaking down contaminants into volatile compounds like H₂O and CO₂—enable efficient cleaning and surface preparation while mitigating the risk of substrate damage.
Samco’s advanced plasma systems are designed to handle both flat and non-flat samples, ensuring optimal results for a wide range of applications, including microelectronics, medical devices, and more. The systems also excel in removing tough resists such as SU-8, PMMA, and Novolac resin, offering flexibility for diverse operational needs without compromising substrate integrity.
Low-damage ashing
Plasma ashing employs ions and radicals generated in plasma to remove photoresist. This process uses two primary mechanisms:
- Physical sputtering by ion bombardment.
- Chemical reactions forming volatile molecules like H₂O and CO₂.
While ions physically bombard the surface to remove photoresist through sputtering, radicals chemically react with the photoresist to form volatile molecules such as H₂O and CO₂. The combination of these two mechanisms is fundamental to plasma ashing via reactive ion etching (RIE). However, one drawback of the RIE process is the potential for plasma-induced damage to the substrate. Reactive ions can directly interact with the substrate surface, leading to physical damage and surface charging.
Cleaning Modes: RIE Mode and Plasma Etch Mode
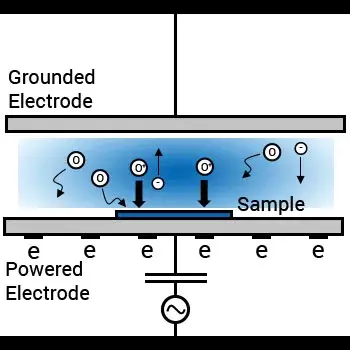
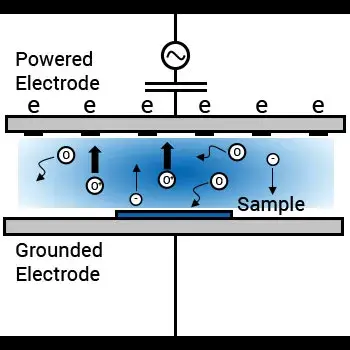
While effective, reactive ion bombardment in traditional Reactive Ion Etching (RIE) can risk substrate damage. Samco addresses this with two plasma cleaner modes, mitigating these risks:
- RIE Mode: Samples are placed on a powered electrode, achieving a high etch rate via ion bombardment.
- Plasma Etch Mode: Samples rest on grounded electrodes, avoiding ion bombardment and minimizing plasma damage.
These configurations enable effective removal of various photoresist materials, such as SU-8, PMMA, and Novolac resin, while protecting the substrate.
System versatility
Samco’s plasma ashing solutions are designed to accommodate a variety of wafer sizes, ranging from 100 mm to 450 mm, making them suitable for both R&D and mass production environments. Optional stage heating enhances the etch rate by enabling precise control of process temperatures, ensuring efficient removal of photoresist across multiple applications. With systems configured for bench-top use and fully automated production lines, Samco provides tailored solutions for diverse operational needs. Whether for small-scale experiments or high-throughput manufacturing, these systems deliver consistent, high-performance results.
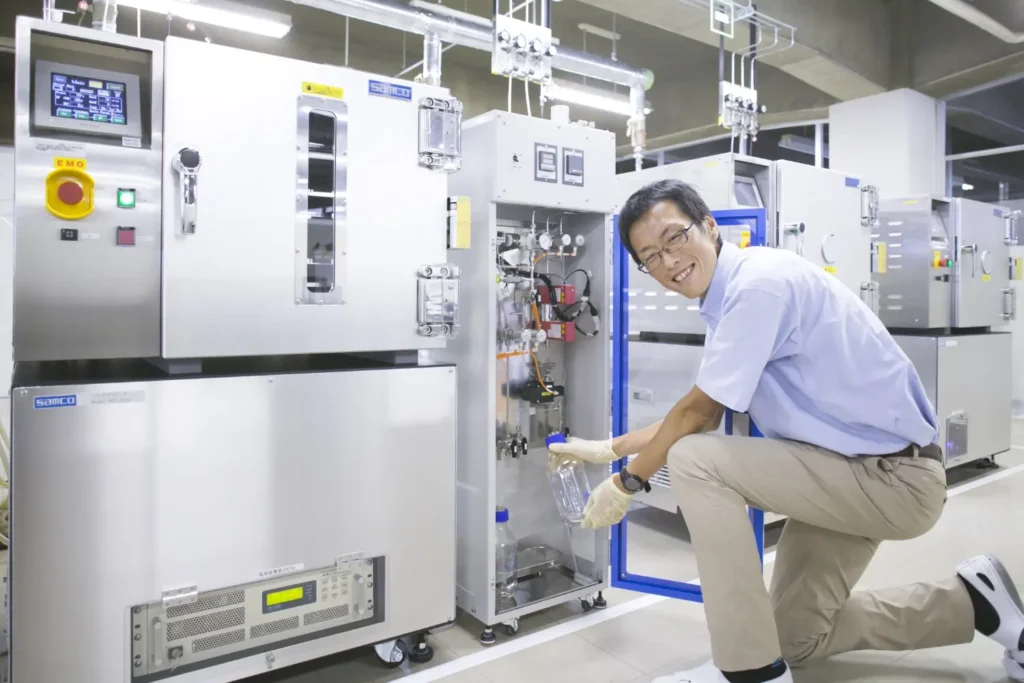
Enhancement of wettability and adhesiveness of resin, metal, and glass by forming polar groups or removing organic contaminants, thereby increasing surface tension and improving adhesion.
Products
Effective removal of organic smear from the bottom of via holes in printed circuit boards, replacing traditional chemical cleaning methods. The process revealed a roughened copper surface, eliminating the need for chemical treatments and costly ancillary equipment.