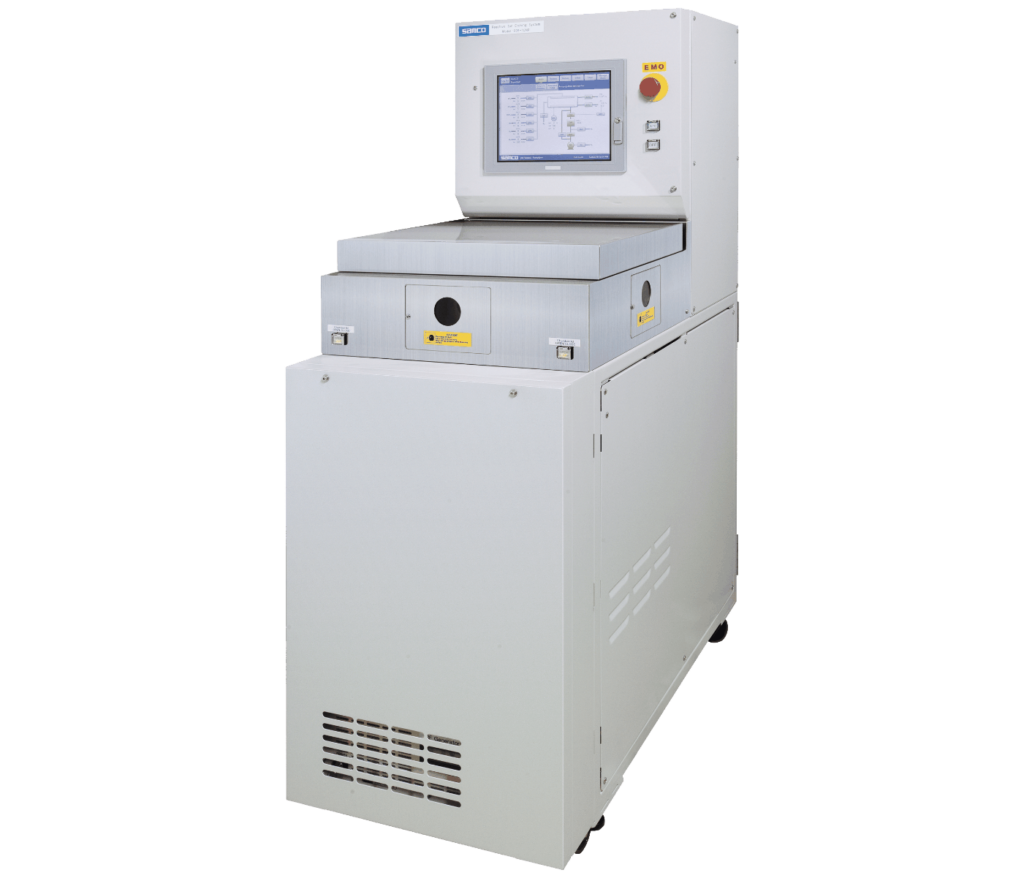
Samco offers reliable and durable Reactive Ion Etching (RIE) systems for R&D and production customers. Our benchtop compact RIE etcher is a suitable tool for academic device research and die deprocessing for IC failure analysis. Samco’s open load RIE systems and load lock RIE systems have a wide process window for plasma etching of various materials (silicon, dielectrics, compound semiconductors, metals, polymers and photoresist). The cassette loading RIE systems improve process throughput for device fabrication.
RIE System Lineup
Key Features & Benefits
- Highly selective anisotropic etching meets demanding process requirements
- A symmetrical evacuation design improves etching uniformity
- Fully automatic “one-button” operation with full manual override
- A computerized touch screen provides a user-friendly interface for parameter control and storage
- Automatic pressure control that allows for precise control of process pressure independent of gas flow
- Dry pump and system layout allow for ease of maintenance
- 13.56 MHz RF generator with automatic matching delivers excellent process repeatability
- Sleek, compact designs require minimal cleanroom space
Applications
- Etching of various materials such as Si, SiO2, SiN, Poly-Si, GaAs, Mo, Pt, Polyimide, etc.
- Removal of various types of passivation films
- Selective layer etching in failure analysis
- Photoresist ashing, stripping, and descuming
- Surface modification (wettability and adhesion improvement)
- Surface treatment of glass substrates, etc.
- Removal of organic contaminants