Introduction
Samco Inc., established in 1979, has been a leading provider of plasma CVD systems and practical process technologies. In recent years, the company has focused on developing innovative equipment, encompassing film stress control utilizing dual frequencies and the integration of VHF band frequencies. In production, Samco has greatly improved film deposition stability and reduced takt time through dry cleaning, receiving widespread acclaim from its clientele. This report is dedicated to presenting the PD-2203LC, a three-chamber CVD system tailored for both production and research applications.
Equipment Specifications
The PD-2203LC is a CVD system integrated with three reaction chambers (RC), incorporating the established functionalities of the PD-220NL CVD system. Photo 1 exhibits the system’s external configuration. This system offers options of either an atmospheric cassette chamber or a vacuum cassette chamber. The vacuum cassette chamber is preferable for direct wafer transfer, while the atmospheric cassette chamber is recommended for tray transfer, as it expedites heat dissipation in the post-process atmosphere. For research applications, distinct film types can be deposited within each reaction chamber, mitigating contamination effects. For production needs, the same film type can be processed simultaneously in three reaction chambers, effectively reducing the takt time per cassette.
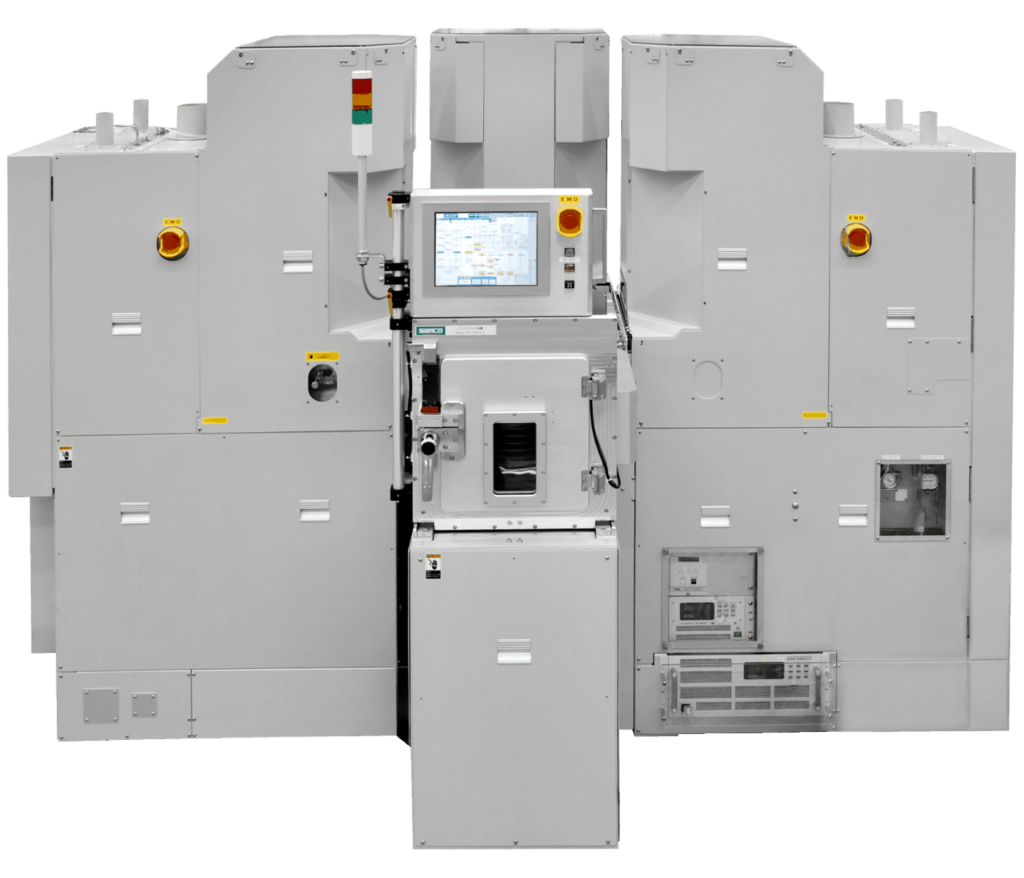
In addition to SiH4, SiO2 and SiN can be deposited using liquid source materials such as TEOS and SN-2™. The implementation of 13.56 MHz and 400 kHz superimposed dual-frequency processes provide excellent stress control by utilizing ionic deposition at 400 kHz. Moreover, the usage of higher frequencies in the VHF band—27, 40, or 60 MHz—instead of 13.56 MHz, generates a high-density plasma, facilitating a faster deposition rate and utilization of radical reactivity in the process.
Deposition Data
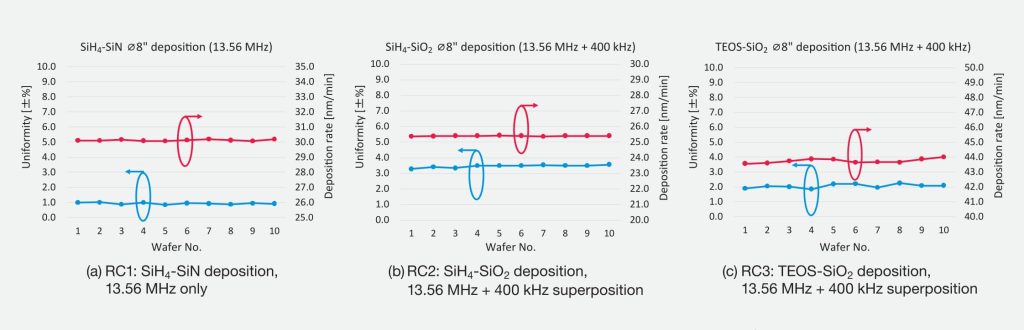
Figure 1 illustrates the deposition outcomes utilizing PD-2203LC. Using 8-inch wafers, deposition of SiH4-SiN solely at 13.56 MHz in RC1, SiH4-SiO2 with dual-frequency deposition in RC2, and TEOS-SiO2 with dual-frequency deposition in RC3 was carried out for ten consecutive batches each. The uniformity of the SiO2 films in RC2 and RC3, affected by the dual-frequency deposition, indicates slightly higher uniformity values. However, it is evident that in both processes, the uniformity and deposition rates remain highly stable throughout ten consecutive batches.
Conclusion
The three-chamber CVD system “PD-2203LC” can use SiH4 gas or liquid source materials for film deposition, with adjustable frequency for diverse applications. In production contexts, the internal components of the reaction chamber are engineered to minimize contaminant adhesion, facilitating efficient dry cleaning. Consequently, it reduces the frequency of opening the reaction chamber to the atmosphere annually, ensuring optimal maintainability.
Adhering to our management philosophy of “contributing to global industrial science through thin-film technology,” we remain committed to advancing equipment and processes for the progression of science and industrial technology.