Nasir Basit, PhD.
Managing Director, NUFAB, Northwestern University
During this interview, we had the opportunity to speak with Dr. Nasir Basit about his journey as Managing Director at Northwestern University’s nanofabrication facility, NUFAB. He shared insights into the facility’s history, its pivotal role in supporting advanced research in fields like bioelectronics and quantum devices, and his experiences in cleanroom management.
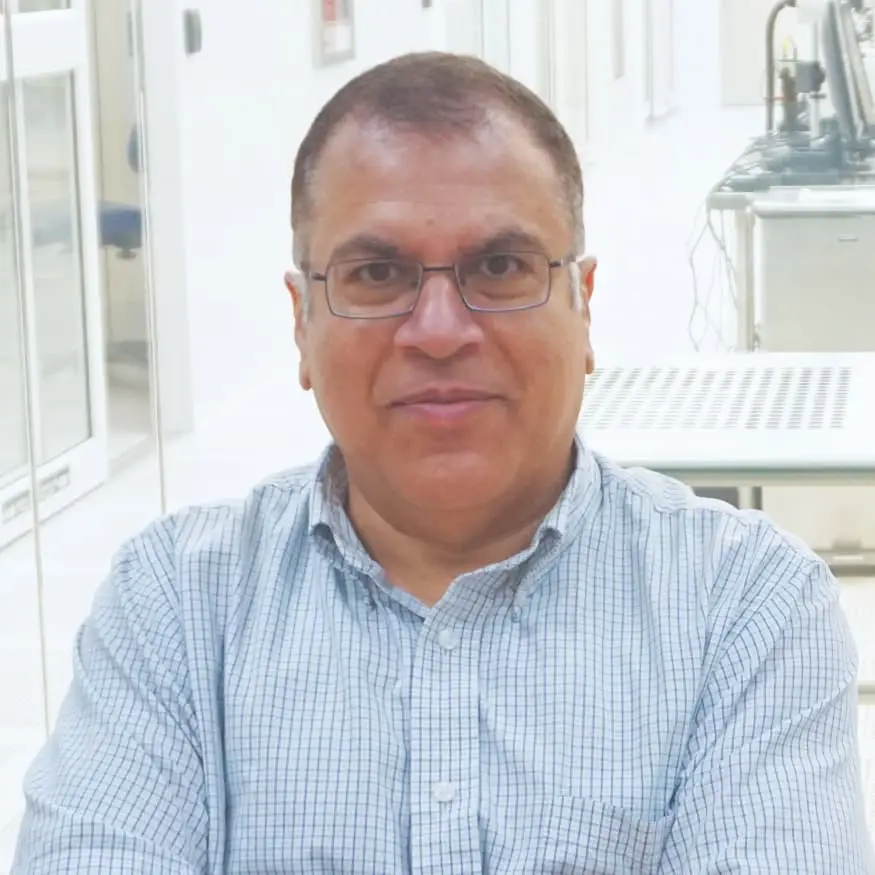
Brief History
1993 – 1998
Doctor of Philosophy (Ph.D.), Electrical Engineering, University of Pittsburgh
1999 – 2002
Research Associate, Texas A&M University
Mar. 2002 – Aug. 2006
Research Engineer, University of Texas at Arlington
Sep. 2006 – Jan. 2007
Cleanroom Manager, University of Texas at Arlington
Feb. 2007 – Jun. 2008
Manager of NanoFAB, University of Texas at Arlington
Jul. 2008 – Present
Director of NUFAB, Northwestern University
NUFAB is the micro/nano fabrication facility at Northwestern University. Can you tell us a little bit more about NUFAB?
NUFAB started in 2010. I moved here to Northwestern in 2008 to start this new facility. They were going to call it “Tech Cleanroom” based on the building name. Since it was meant to be a central facility for the whole university, I changed it to NUFAB, which is Northwestern University’s Micro and Nano Fabrication Facility, and it has grown by leaps and bounds since then, about 16 years later.
For the first few years, we were in a refurbished cleanroom in this same building. Our first Samco tool, an RIE-10NR, was actually purchased before we completed the new cleanroom, and we moved it here in fall of 2013. Once we were settled in the new facility, we continued to expand our toolset. In 2015, NUFAB was integrated with the NUANCE Center, which was established in 2001 and currently manages over 100 analytical and characterization capabilities. By adding our nanofabrication to NUANCE’s imaging and analysis expertise, researchers can now fabricate and fully characterize materials and devices in one place; this integration has significantly boosted innovation and collaboration across disciplines.
How many tools are there in the NUFAB facility?
Currently, NUFAB operates in two locations: this main facility and a second location in Cook Hall. Between the two sites, we have nearly 100 tools dedicated to both fabrication and characterization. This facility encompasses 7,000 square feet, while the Cook Hall cleanroom has 2,000 square feet. Both are Class 100 cleanrooms.
What are some of the process capabilities of NUFAB? What systems and processes do you support here?
NUFAB supports both micro- and nanofabrication processes, offering a range of advanced fabrication and characterization tools. Our fabrication capabilities include deposition systems, etching systems such as reactive ion etching and deep reactive ion etching, furnaces, and a variety of patterning tools, including photolithography and e-beam lithography. For characterization, we offer electrical characterization and imaging tools, including reflectometry, ellipsometry, and profilometry, with scanning electron microscopy (SEM) and focused ion beam (FIB) tools under installation. Additionally, we provide laser patterning and cutting tools for microfabrication.
How many users use the NUFAB facility? What are some of the major areas of research of the users?
NUFAB currently has nearly 400 active users. This represents significant growth from our first year, when we had only 10 to 20 users. Our user base is diverse, including graduate students, undergraduates (even as early as their sophomore year), and postdoctoral researchers. These groups are roughly equally represented among our users. We also serve external users and provide services to those outside the university. There are 2 fast-growing research areas among our users, first; bioelectronics (including sensors and biomedical devices) and second; quantum devices. We also support researchers working in the more traditional fields of photonics and electronics.
Are there any plans for expanding the facility or acquiring new tools in the future?
Space is becoming a constraint in both cleanrooms, particularly for process tools like deposition and etching systems. However, a new engineering building is planned for construction in the next five years, and we are developing plans for a new nanofabrication facility within that building.
What are NUFAB's short-term and long-term objectives? What are your goals in terms of supporting users?
Our focus is on supporting the growing areas of biomedical devices (including sensors and diagnostic techniques) and quantum devices. To achieve this, we’re acquiring tools that cater to these specific needs. For example, we’re investing in tools capable of handling flexible substrates and performing deposition and etching at lower temperatures, which is crucial for bioelectronics research. For quantum research, we’re acquiring ultra-high vacuum (UHV) tools.
Where do you see NUFAB in ten years?
In ten years, I envision NUFAB continuing its growth trajectory. Northwestern’s strong research programs across various disciplines, particularly its robust medical school, attract faculty interested in cutting-edge fields like bioelectronics and quantum devices. This, in turn, drives the demand for our services.
Before NUFAB, researchers had to rely on external nanofabrication facilities. Since our establishment, we’ve experienced consistent growth in equipment, users, and staff, and we anticipate this trend will continue. The expansion of our cleanroom, even amidst challenges like the COVID-19 pandemic, exemplifies our commitment to meeting the evolving needs of our users.
Looking ahead, I expect biomedical and quantum research to remain key areas of focus for NUFAB. However, CHIPS Act that is tailored to bring most advanced semiconductor manufacturing back to US may result in new fabrication and work force development capabilities at Northwestern. We are committed to providing state-of-the-art resources and support to researchers in these fields and beyond.
We are part of the National Nanotechnology Coordinated Infrastructure (NNCI), a nationwide program funded by the National Science Foundation (NSF). The funding cycle spans ten years, with renewals occurring every five years. Having just completed the current ten-year cycle, we must reapply next year to secure funding for an additional ten years. The NNCI program operates at a national level through 16 nodes, comprising universities geographically distributed across the United States. In the Midwest, we serve as the lead institution in collaboration with the University of Chicago.
NNCI program supports significant outreach efforts, including workforce development for local small colleges and engagement with regional industries, enabling them to become part of our external user community. Additionally, small companies lacking access to advanced fabrication facilities benefit from utilizing these resources for startup research. Our facilities are accessible to researchers worldwide, with some users coming from outside the United States. With the continuation of this program, we aim to further expand these collaborations and extend our global impact.
Could you tell us about your background in the semiconductor industry and how you came to be involved with NUFAB?
My path in microfabrication began with my PhD studies at the University of Pittsburgh. After graduating, I sought hotter climates and pursued postdoctoral work at the University of Texas at Dallas, where I gained experience in their cleanroom. I later transitioned to the University of Texas at Arlington, where I took on the responsibility of managing their new cleanroom facility. This role provided valuable insights into equipment installation, process development, user training, and facility management.
Although I hadn’t planned to relocate, an opportunity arose at Northwestern University in Chicago. They were in the initial stages of planning NUFAB, and my expertise in cleanroom management aligned well with their needs. I joined Northwestern, and the rest, as they say, is history.
NUFAB acquired its first two Samco systems, the RIE-10NRs, back in 2009. How have those systems been utilized?
Those RIE-10NRs have truly been our workhorses! When I joined Northwestern in 2008, I was tasked with renovating the old cleanroom. While selecting equipment, I came across Samco. At the time, they were relatively new to the university market, and references were scarce. To minimize risk, I decided to acquire two of their smaller systems, the RIE-10NRs.
These systems have proven to be incredibly versatile. They’ve been used for etching silicon in various applications, etching III-V materials like GaAs and GaN, and for resist removal or stripping, and many more applications. To accommodate the high demand for resist removal, we later added a Samco PC-300 plasma cleaner. Both the RIE-10NRs and the PC-300 are used by nearly every research group in the cleanroom, across all research areas.
What were the key factors that influenced your decision to acquire the PECVD and Bosch DRIE systems from Samco?
Our previous experience with the Samco RIE-10NRs was a major factor. Those systems have been incredibly reliable, with minimal downtime. In a university setting, equipment reliability is paramount. Our research depends heavily on these tools, and any downtime disrupts projects and can be discouraging for users.
When we were evaluating options for the PECVD and Bosch DRIE, we considered both Samco and other established companies. Ultimately, our positive experience with Samco’s reliability, customer service, and the performance of the new systems solidified our decision.
What are some of the operational, financial, or technical challenges you face at NUFAB?
Our primary challenge is ensuring continuous equipment operation. As a core facility with limited resources and space, we can’t afford redundant systems. Equipment reliability is absolutely essential. Any downtime disrupts research, delays projects, and can frustrate users.
Financially, maintaining a state-of-the-art facility requires significant investment. Northwestern provides strong support, but we are constantly seeking alternative funding sources, such as industry partnerships and philanthropic grants, to enhance our capabilities and expand our resources.
You've clearly had a positive experience with Samco systems. Would you recommend them to others, and what advice would you give to someone considering a Samco tool?
Based on my experience with the RIE-10NRs and now the PECVD and Bosch DRIE, I would definitely recommend Samco. Their systems have been reliable and robust, which is crucial in a research environment. However, I always advise people to consider their specific needs and do their due diligence. What works well in one facility might not be the best fit for another. I encourage potential buyers to ask detailed questions about the system’s capabilities, maintenance requirements, and customer support. Ultimately, the best recommendation comes from firsthand experience. I’m happy to share my experiences with Samco, and I believe their systems offer strong performance and reliability.
Looking back over the years, are there any particular achievements or moments at NUFAB that stand out?
Several come to mind. Being involved in the design of the NUFAB cleanroom was a significant accomplishment. I was able to leverage my previous experiences to influence the layout and features of the facility, ensuring it met the needs of our researchers.
Another proud moment was successfully relocating all of our equipment from the old cleanroom to the new facility in just one week, minimizing downtime for our users. Attracting renowned researchers like John Rogers to Northwestern has also been a major highlight. His decision to relocate his research group here was a testament to the capabilities and reliability of NUFAB.
More recently, securing the BioHub, led by Shannon Kelly, in partnership with the Chan Zuckerberg Initiative, has been another exciting achievement. These successes demonstrate the growing reputation of NUFAB and our ability to support cutting-edge research.
Do you have a motto, philosophy, or favorite saying that you live by?
Never give up.
Favorite meal?
I like anything when I am hungry, but I especially enjoy spicy food. I generally like all kinds of cuisine, including American, Italian, Chinese, and Japanese (excluding raw fish), and I will usually add spice to those as well. There’s a great place on Devon Avenue with Pakistani and Indian food that I love.
Any hobbies outside of work?
I like to stay active. I enjoy fixing my car, doing yard work, and even some home renovation projects. I’m a hands-on person, which is something I appreciate about my work at NUFAB as well. Some people might prefer to sit at a computer all day, but I enjoy working with the equipment and collaborating with students in the cleanroom.
Any other thoughts you'd like to share?
Just to express my appreciation for Samco’s support. I hope they continue to provide excellent service. And please do stay in touch!
We appreciate your time and insights. We look forward to continuing our strong support of NUFAB.
Process capabilities of Samco's Si DRIE Systems
Samco’s silicon deep reactive ion etching (Si-DRIE) systems utilize both the Bosch and Non-Bosch processes to enable precise fabrication of trenches, holes, and pillars for various device applications. Below are examples of structures fabricated using these techniques:
- Bosch Process for Micro Fabrication
- Non-Bosch Process for through-silicon via (TSV)