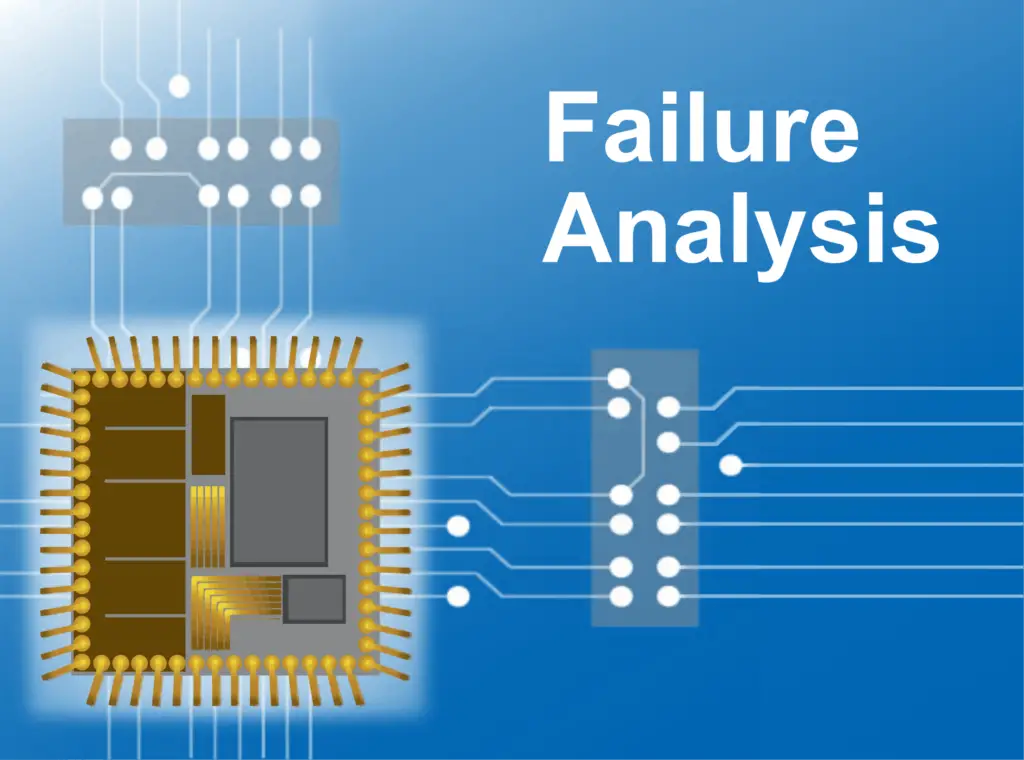
Samco provides advanced solutions tailored for IC failure analysis to enhance device reliability and pinpoint failure modes. Leveraging decades of dry etching expertise, Samco’s systems are used globally in both production and failure analysis (FA) labs, offering precise etching that meets the stringent demands of modern semiconductor manufacturing.
Our layer removal processes allow the exposure of up to 5 metal layers without risking delamination or erosion, ensuring dependable and repeatable results. With options ranging from die to 300 mm wafer processing, Samco’s systems are equipped with cutting-edge features like endpoint detection for precise, reproducible etch stops.
Plasma Etching Solutions
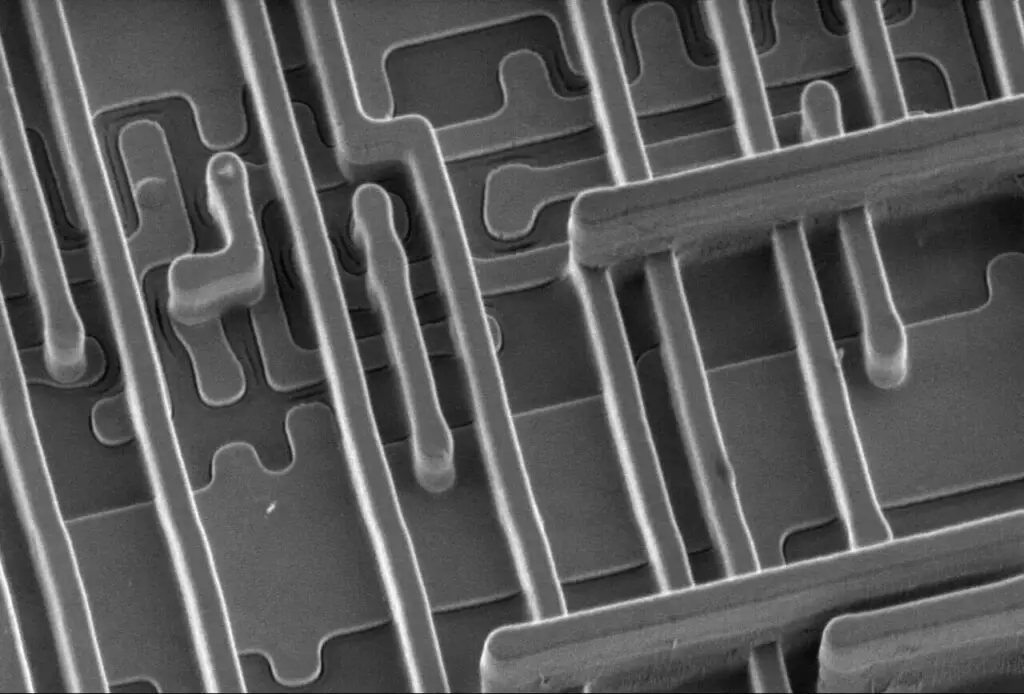
Our plasma etching process enables high-selectivity, high-aspect ratio etching across a diverse range of materials, facilitating targeted passivation removal, defect decoration, and layer-by-layer inspection for accurate failure analysis.
- Material compatibility: Samco’s systems handle materials including silicon (with BOX etch stop), borosilicate glass, PSG, BPSG, and low-k dielectrics. Our selective etching approach also supports polymer removal, meeting diverse failure analysis requirements.
- Exposure without erosion: Reliable removal of up to 5 layers without compromising the integrity of underlying Al or Cu lines enhances inspection accuracy and reliability.
- Scalable decapsulation: from Die to 300mm
- Precise and repeatable etch stop: Samco’s optional endpoint detection system offers automated, precise thickness monitoring for transparent films like oxide and nitride, enabling full process control and repeatability.
- Trusted worldwide for FA labs: Offering unmatched precision and reliability, supporting everything from prototyping to high-volume manufacturing.
Enhanced material removal
Using advanced plasma etching technology, Samco’s systems are compatible with the following materials:
Silicon (Si)
- Etch stop at Buried Oxide (BOX)
Oxides
- Borosilicate Glass (BSG)
- Phosphosilicate Glass (PSG)
- Borophosphosilicate Glass (BPSG)
- Etch stop at bulk Si
Nitride
Inter Metal Dielectrics (IMD)
Inter Layer Dielectrics (ILD)
Low-k Dielectrics
Polymers
- Polyimide
- Epoxy
- Other polymer films
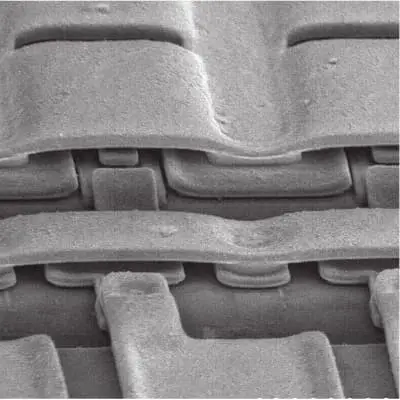
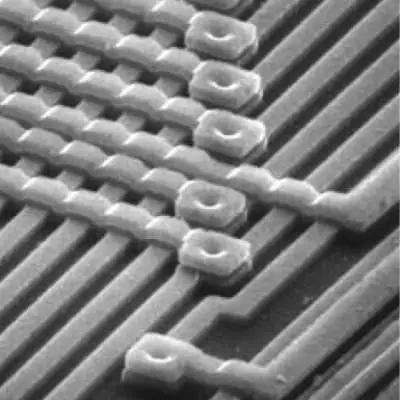
Selective etching without delamination or erosion
Reliable removal of up to 5 layers without compromising the integrity of underlying Al or Cu lines enhances inspection accuracy and reliability. This technique enables layer-by-layer depassivation and failure inspection of complex-structured dies.
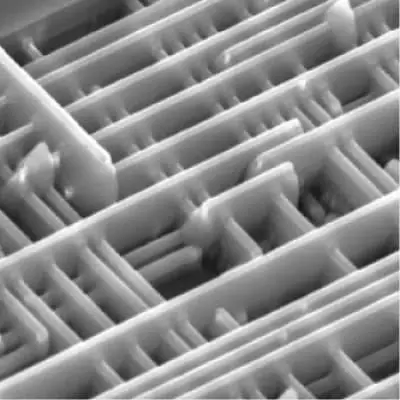
Scalable system lineup
Samco’s plasma etching systems provide a comprehensive lineup from table-top RIE systems for single dies to large-chamber systems for up to 300 mm wafers. With open-load RIE options for low ownership costs and ICP systems for low-bias power processing, we cater to diverse customer needs.
- Scalable Options: Choose from economical open-load options, robust ICP etching systems for low-damage processes, and large-chamber systems for high-throughput requirements.
- Charging and Physical Damage Prevention: Low bias power processes in our ICP systems mitigate charging and mechanical damage on delicate die structures.
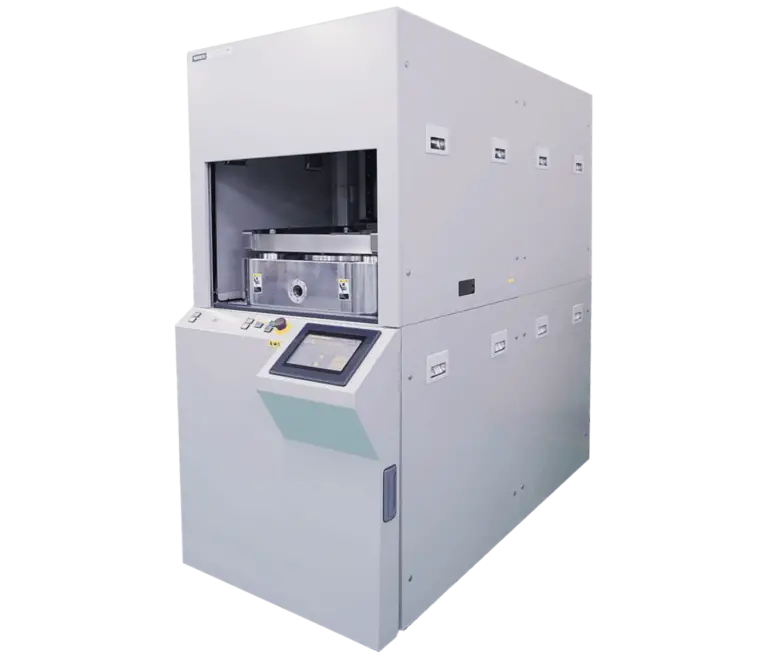
Precise and repeatable etch stop
Reliable endpoint detection is essential for consistent, high-quality etching. Samco’s optional endpoint detection system offers automated, precise thickness monitoring for transparent films like oxide and nitride, enabling full process control and repeatability.
- Automated Monitoring: A camera with an X-Y stage continuously measures refractive index changes directly above dies, ensuring consistent, reproducible results.
- Quality and Reliability Improvement: Proven in both R&D and high-volume manufacturing, Samco’s plasma processes support quality enhancement and reduce device failure rates.
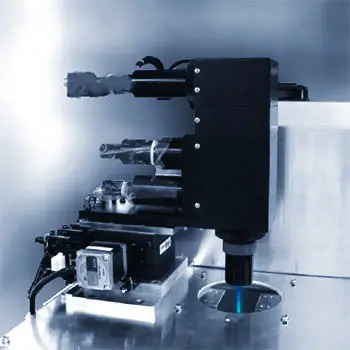
Benefits for failure analysis labs
Samco’s plasma decapsulation solutions offer unmatched precision and reliability, supporting everything from prototyping to high-volume manufacturing. Trusted globally, our systems provide:
- High Selectivity and Low Erosion: Ensuring delicate structures remain intact.
- Flexible System Options: Solutions from die level to full wafer processing, tailored to diverse needs.
- Precise Process Control: Automated endpoint detection ensures reproducibility, essential for in-depth FA applications.
Defect analysis of exposed 5-layer Al wiring using RIE plasma etching system; successfully removing silicon nitride (SiN) passivation layer and silicon oxide (SiO₂) interlayer insulator, preserving the underlying Al wiring.